Living Happily Ever After With Your Cell Therapy Facility: Managing Innovation & Your COGS

By Anna Rose Welch, Editorial & Community Director, Advancing RNA
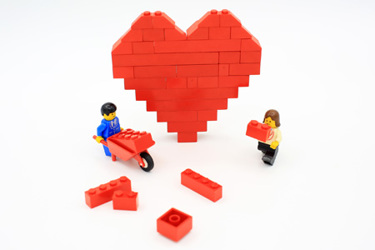
In recent months, I watched an Endpoints News webinar entitled, “Strategies For Building A Cell Therapy Manufacturing Facility.” The webinar, which included executives from Tenaya Therapeutics, Iovance, Kite Pharma, and Instil Bio, provided some great considerations and best practices for those of you who have chosen to take the plunge into building your own capacity.
Because the C&G space is a wild adventure, to say the least, I wanted to share these experts’ insights in a less traditional way: via a (very simple) “choose your own adventure” series of articles. This “adventure” addresses the following scenario:
After an afternoon of manufacturing facility-related conversations over birdwatching, a walk through the park, ice cream, and coffee, you’re just preparing to head back to your office when you find yourself smack dab in the middle of another interesting conversation between Scott Bertch, executive director, clinical site head of Tenaya Therapeutics, and Faraz Siddiqui, VP, process development & manufacturing operations for Instil Bio. It turns out, they were on a panel discussion together, during which they were asked about the manufacturing innovations they expect will improve manufacturing efficiency and overall cost of goods sold (COGS). Though your facility isn’t even built yet, you’re all ears — because, really, who doesn’t love a good crystal ball-style question?
Though it’s always exciting to focus on the much-needed technological innovations that are still a few years down the line, Faraz homes in on the here-and-now. Specifically, he argues that striving for operational efficiencies and a higher utilization rate — though (arguably) less sexy than innovative technology — will make the most immediate impact on a company’s overall COGS.
“I don’t care how innovative your facility is and how beautifully you’ve integrated all the systems,” he says to you and Scott. “If that facility’s capacity utilization is at 50 percent, there’s no way you’re going to make up for the cost that you’re incurring. You need to have a good handle on operations to avoid over-investing in capacity and a workforce that will be sitting idle, waiting for a product to be manufactured.”
Looking long-term, Faraz anticipates that companies will need to focus their efforts on evolving systems engineering and IT infrastructure. Such efforts will be integral to establishing control over the manufacturing process, as well as managing the data that will permit timely decision-making. Exception-based reviews is the goal, Faraz acknowledges, but that data management infrastructure will need to be in place to make that future a reality.
Scott is quick to agree, adding that the industry is already challenged to make sense of that data today, given just how much is available thanks to rapidly improving technologies.
“The amount of data you can get out of systems is incredibly useful,” he qualifies. “However, that data has to be put together in such a way that you can get to it and use it to make meaningful, quality-based decisions.” Many of the systems today produce a wealth of data, but companies are challenged to filter through and single out what data will be the most important.
“Data for the sake of having data is not as useful as getting key pieces of data into the right people’s hands when you need them,” he adds.
In addition to IT and data infrastructure, Scott also points to the benefits that closing your process can have on the overall physical infrastructure and cost of running your facility. Lower class clean rooms provide benefits in spades, making the day-to-day flow of people, the technology, and contamination control procedures much less onerous. Taking the necessary steps to limit contamination in the manufacturing process will be time well-spent, he emphasizes, as it is a sure-fire way to reduce overall risk and, in turn, lower those pesky COGS.
Just as Scott concludes his thought, your phone starts to ring. Your boss has finally tracked you down. (Le Sigh.) After thanking Scott and Faraz for sharing their thoughts with you (more than once today!), you shake their hands and start to walk down the street. When you woke up this morning, you couldn’t have anticipated such a whirlwind afternoon of chance encounters and knowledge sharing. You make a mental note to take more walks when you’re facing future manufacturing challenges — who knows which manufacturing experts you may run into when you least expect it...