Bluebird Bio FDA AdCom: For Cell & Gene Manufacturing, FDA Approval Is Just One Of Many Milestones

By Anna Rose Welch, Editorial & Community Director, Advancing RNA
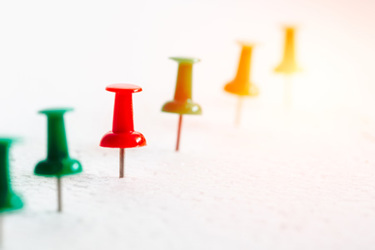
Editor’s Note: This is the final installment of a three-part series discussing the main takeaways from bluebird bio’s recent FDA AdCom evaluating its two ex-vivo gene therapies: eli-cel in cerebral adrenoleukodystrophy (CALD) and beti-cel in β-thalassemia. If you missed the previous two articles, you can check them out here — Risk Vs. Benefit A “Living” Measurement For Commercialized CGTs and Your Viral Vector’s Future Is In The Eye Of The Beholder
If you tuned in to any of bluebird bio’s FDA AdCom meeting, you’ll know that these hours-long conversations left no stones unturned in evaluating the clinical profiles of both eli-cel and beti-cel gene therapies. As the FDA’s Bryan Wilson told us at the very beginning of the AdCom meeting, CMC was not going to be covered during the two-day-long evaluation of these therapies’ clinical benefit/risk profile. However, given the close relationship between how a therapy is made and its clinical performance, it’s not surprising that the committee found it difficult to dive deeply into the clinical results without venturing into certain aspects of the manufacturing process.
Overall, this two-day march through the clinical data served as a great case study for all other CGT companies striving to bring their therapy — and its manufacturing process — before the FDA and/or its advisory committees. Though there were no presentations or Q&A sessions dedicated exclusively to the company’s CMC approach, the AdCom did reveal (albeit in small snippets of conversation) how bluebird’s understanding of process and product improved over the course of development and could continue to be even better understood following commercialization.
This growth in understanding was best depicted in the numerous conversations around the “transduction efficiency” of both therapies. On the one hand, this attention is reflective of the fact that HSCs are one of the most notoriously difficult cell types to transduce. As one of bluebird’s analytical leads shared, it used to be said that HSCs were impossible to transduce. (Pro tip: the best way to figure something out is to say that it can’t be done. Entire industries have been built around this claim.)
But more importantly, transduction efficiency was found to be tied closely to the clinical impact of each therapy. In fact, as the company shared, three of the six potency assays for eli-cel are dedicated to transduction efficiency (namely % of cells transduced, vector copy number [VCN], and VCN per transduced cell). For eli-cel, the higher the VCN the more potent and efficacious the therapy was. For beti-cel, the four patients that did not achieve the trial’s primary endpoint — transfusion independence — all had a lower percentage of transduced cells in their drug products.
This beti-cel example is worth looking at a bit more closely — not only because of how bluebird addressed this issue, but because it nicely depicts the tight-rope we are constantly walking between control and flexibility in the CGT manufacturing space.
When asked how the company interpretated the data behind the four beti-cel patients who didn’t achieve transfusion independence, a bluebird executive pointed specifically to the manufacturing process. Following a retrospective analysis of the data, the company felt some of its manufacturing parameters were contributing to these lower transduction rates. As such, it tightened several of its manufacturing parameters and adjusted its acceptance criteria for the percentage of transduced cells. It should be noted that all patients treated following this manufacturing adjustment have achieved transfusion independence. In fact, the percentages of cell transduction in each of their drug products were also on the higher end (between 80-95 percent).
Perhaps it goes without saying that, for a CGT company in particular, arriving at the BLA “finish line” doesn’t mean your analytics and manufacturing paradigm are perfect. Now, don’t get me wrong: to get this far, bluebird had to do its analytical homework — and then some. But this AdCom revealed just how far we can come — all the way to approving a novel therapy — while still having so much yet to learn.
As the FDA’s Bryan acknowledged, the company and FDA are still actively collaborating on lingering CMC issues in the company’s programs overall. The committee also had additional recommendations for the company as it (hopefully) advances both eli-cel and beti-cel from the clinic to the market. In particular, several committee members would like to see more data in the long-term to understand how the cell expansion process, high multiplicity of infection (MOI) ratios, transduction, and cryopreservation affect the overall health of the cells in the final drug product. Given that the amount of vector required to attain a high transduction percentage and VCN can have a detrimental effect on the overall health of the cells, one AdCom member encouraged developers to keep striving to achieve a healthier balance between vector toxicity and transduction efficiency. (If you’re interested in reading more on the promise and pitfalls of pursuing transduction efficiency, check out my article with Orchard Therapeutics’ CEO to see how the folks at Orchard are tackling this particular challenge.)
As I listened to this back and forth on tightening manufacturing controls, I couldn’t help but liken the process of advancing a manufacturing process to that of carving a statue out of marble. What starts as an undefined, ungainly chunk of stone will, overtime, be carefully chipped into its final form. There’s no denying that bluebird bio’s AdCom was a highly specialized and individualized deep dive into two unique therapies. But if there is one thing that can be gleaned from the many dizzyingly technical hours it would be this: the arrival to a BLA is a huge milestone for a company, for patient populations, and for a manufacturing process — but it’s hardly the finish line.