The Ties That Bind: Engineering A CGT Manufacturing-Centric Culture

By Anna Rose Welch, Editorial & Community Director, Advancing RNA
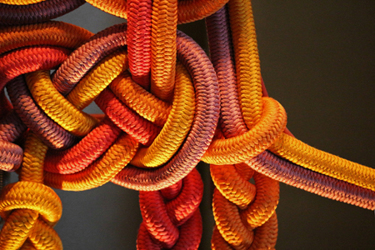
When I met Tenaya Therapeutics CEO, Faraz Ali, we were just starting to emerge from the worst part of the spring 2021 pandemic, by which point navigating the workday from family-filled houses was finally second nature to many of us. This was clearly the case for Ali who carried out our early morning interview in the front seat of his car so as not to wake up his daughters. (Clearly, they have him wrapped around their pinky fingers — as is only right.
In March, Tenaya announced it would be establishing a cGMP AAV manufacturing facility. In addition to boasting several preclinical candidates for rare cardiac diseases, the company also aims to use its AAV gene therapies to treat more prevalent conditions. But before the industry and Tenaya can successfully reach these larger patient populations, there will need to be advancements in the manufacturing paradigm for AAV to produce higher titers upstream followed by greater yields of high-quality vector downstream. There is also a lot of work ongoing — both across the industry and at Tenaya — to engineer novel AAV capsids to ensure that the vector reaches the proper “final destination” in the body. These innovations also introduce complexity and risk to the already difficult task of AAV manufacturing. Changes in the capsid may necessitate changes in upstream and downstream manufacturing processes as well as the analytical assays necessary to properly characterize the final product.
But if we look beyond the strides that must be made in the biological, analytical, manufacturing, and capacity realms, Ali also homed in on how the gene therapy manufacturing paradigm requires a new way of doing business. Players in the pharma industry have gotten incredibly good at identifying their strengths and weaknesses. Acquisitions, licensing programs, manufacturing and commercialization partnerships, and outsourcing partnerships are built around the understanding that one party has expertise and/or physical capacity that the other doesn’t. But in this current day and age of the cell and gene therapy (CGT) industry, Ali made a great point:
“CGT manufacturing is not a nut that any one company and/or CDMO can claim to have cracked,” he explained. “Though we’ve made incremental improvements over time, especially in the production of viral vectors, companies may need to expand their boundaries beyond what is comfortable to be successful.”
There are two ways we can visualize this expansion of boundaries — the most obvious, of course, being the construction of in-house manufacturing capabilities. Those of you taking the infrastructure plunge will know first-hand just how much of a literal expansion this is even beyond square footage/physical footprint/geography. Such a decision also increases the number of necessary employees, operators, equipment, and specialized teams needed to efficiently and smartly use the new GMP space. (In fact, as I wrote in one installment of this “choose your own manufacturing adventure” story, how a growing CGT company manages this influx of new people and operations will be yet another growing pain.)
However, our conversation also revealed a more nuanced definition of a CGT company’s “expansion” of boundaries; from its earliest days, a CGT company must create a culture that understands and appreciates manufacturing for the science that it is.
We have heard time and time again how important it is to have manufacturing experts on board at the launch of a company. Obviously, this will help a company successfully tackle a laundry list of manufacturing challenges — whether it be getting a facility up and running; selecting the right equipment; hiring the right people; and/or producing the therapy for the first-in-human studies. But I liked Ali’s addition to this list; he wanted to make sure Tenaya would be willing to take the necessary risks with cell culture, cell line, and process development and stay the course to welcome manufacturing breakthroughs in the long-term.
“The time and effort you spend on manufacturing innovations might be time and effort you could spend on another product; it will be an opportunity cost,” he acknowledged. “But you don’t want to find yourselves in five years looking back saying, ‘Remember how we were going to work on x, y, z manufacturing breakthrough? Because by then, it’ll be too late. If you weren’t producing the material using, for example, the new cell line, the new bacmid, the new process at the GLP tox level when preparing for the IND, you’re going to have to perform comparability,” he added. (And, as we know, that can be a process wrought with time-consuming challenges in and of itself.)
For CGT companies — many of which are built around cutting edge science and research as opposed to manufacturing science — the seemingly sudden tidal wave of manufacturing hires may not be a well understood transition within an organization. Resources within a new biotech are precious, and hiring GMP manufacturing and quality control teams, as well as planning for a manufacturing facility with all its bells and whistles, will require a big portion of financial resources and company energy. This is why Ali made it a point to unite the R&D and manufacturing teams within Tenaya to ensure each team had an understanding of the other team’s different but equally critical brand of science.
Now, dear reader, I abhor the word “synergy.” (Lauv’s face expresses my feelings here.) However, in this case, I just couldn’t avoid it; what ended up happening from Tenaya’s efforts can only be described as “synergistic magic.” (Last glitter gif, I swear.)
The company set up scientific forums during which the R&D and manufacturing teams converged. At first, these forums were dedicated to introducing the research projects the R&D teams were undertaking. However, these assemblies also allowed members of the manufacturing team to start asking questions and demonstrate their own scientific chops, if you will, outside of the manufacturing world. These forums then opened up the spotlight to the manufacturing experts who presented on the why and how of process optimization — and particularly why some science just doesn’t scale. Couple these interactions with upper level executives sharing the many COGs- and manufacturing-related stumbles CGT companies have faced at the regulatory finish line, and the research and manufacturing teams both discovered what Bruce Springsteen has been singing about in “The Ties That Bind.”
Such forums ultimately encouraged greater coordination and collaboration between research and manufacturing. It wasn’t until Tenaya’s scientists and engineers began having conversations together on how to improve the manufacturing platform as a whole that Ali sat back and said, “Holy moly, we did it.”
“It’s important that manufacturing not be viewed as a commodity,” he concluded. “A CGT company has to build and nurture a culture that appreciates the critical role that manufacturing, along with research, will play in bringing CGTs to more patients. Manufacturing is a science — and a tough science at that — which will only lead to breakthroughs for patients it it’s given the same amount of respect, attention, and investment as a company’s core research.”